在甘肃稀土厂区,有这样一支队伍,他们不怕吃苦,不怕脏活累活,敢于挑战,攻坚克难,以埋头苦干、脚踏实地的行动,默默坚守在生产现场,辅助稀土分离板块达标达产运行。在此次对标赶超活动中,他们积极担当、勇于作为,敢想敢干,创造出多项历史新高,为公司“提质降耗、挖潜增效、开源节流、扭亏脱困”会就了一笔浓墨重彩,它就是公司稀土生产线的保驾护航单位——试剂车间。该车间有58名职工,看似虽小,但却有着大的担当,他们承担着公司稀土生产过程中氨氮废水的环保处理及资源化利用工作,是稀土生产链条上一个不可或缺的车间。
寻找“突破口”和“挖潜点”
自8月份,公司在全厂范围内吹响对标赶超集结号后,试剂车间第一时间响应,迅速组织车间班子成员、职能人员、班段长、生产骨干召开动员大会,利用黑板报、车间安全生产微信群、党员大会、车间晨会、班前班后会等形式,给全体职工讲形势、谈问题、提措施、明任务、比奉献,号召车间全体职工发挥聪明才智,共同寻找车间对标赶超活动的“突破口”和“挖潜点”。通过对1-7月份车间生产经营全面、系统的分析研究,大家一致认为现有氨氮废水处理装置工艺设计缺陷、处理能力不足、氯化铵产量低是造成蒸汽单耗高,废水处理成本居高不下的关键问题,也是车间挖潜增效的主要“突破口”和“挖潜点”。
技术改造 激发对标活力
在找到“突破口”和“挖潜点”后,试剂车间立即组织车间工程技术人员、班段长、职能、维修人员组成攻关小组,针对现有的生产设备、管道设施,从保证安全生产、提高废水处理能力、降低工人劳动强度、改善工作环境、现场文明生产、发挥设备效能、延长设备使用寿命七个方面制定技改措施。
纯水岗位根据原水水质及时调节浓水、纯水产出比,调整次氯酸钠、亚硫酸氢钠等水处理药剂添加量,确保收率达到75%,供出产品合格率100%;精制氨水岗位通过改造完善挥发出来的氨水回收管道,减少氨气挥发对环境的污染和对人体的伤害;深度水处理岗位用一级浓水代替一次纯水冲制氨水,每天可减少进蒸发器的杂水20~25m3,在Ⅱ蒸发器与Ⅳ蒸发器之间增设DN200管道,使Ⅱ蒸发器内的高温气体进入Ⅳ蒸发器,Ⅳ效蒸发器温度由原来的46℃提升52℃,加快蒸发速度,缩短氨氮废水在蒸发器内的蒸发时间,从而达到单位时间内增加废水处理量的目的,每月节约费用1.2万元;由于用水单位的不均衡性,造成中水储存和供出能力不足,车间通过安装管道阀门、优先外供中水等措施,增加中水储存和供出能力;为了延长离心机的使用寿命,年初将应更新的离心机,采用报废离心机上的部分完好部件与新采购的一些新备件,重新修复,组装了一台离心机用于生产;为改善氯化铵包装间的工作环境,将两台换热器及分汽缸等,从室内移至室外,从而使包装间内的温度平均下降20℃左右,改善了岗位工人在夏季高温时间段身处40~50℃的工作环境;为解决氯化铵产品长期不稳定的因素,车间工程技术人员,对上游各车间所供氨氮废水中的杂质影响蒸发处理量进行定量实验分析,通过实验论证,氨氮废水中的Na、SO42-、稀土等杂质严重制约着蒸发浓缩的速率和析出晶体的物状。经车间技术组人员研讨过后,规定每班第二批料出完后,用原水浸泡一效蒸发器,以保障蒸发系统连续稳定有效的运行。
细化考核 推动对标升级
试剂车间领导班子结合实际、把握重点、分解目标、强化落实、严格考核,把氨氮废水处理量、氯化铵产量和吨水蒸汽单耗作为重要对标指标,分别与工资总额的30%、30%、40%挂钩,将设备管理人员和维修人员的工资分别挂钩进行考核;把纯水的收率、产量和动力消耗也作为主要对标指标分解落实,中水的产量及动力消耗分别按50%、40%、10%挂钩考核并计提工资,变压力为动力,让每一名职工身上都感受压力。结合现场安全标准化管理、能源消耗定额管理、日常工作任务的安排和完成情况,对于不能胜任本岗位作业的人员实行二岗工资考核,岗变薪变,并制定出三条措施:强化车间统计核算和经济责任考核作用,建立各班组材料消耗、原水消耗、蒸汽、电耗、产品及单耗台账,建立日报、周报制度,盯住班产、日产及时统计分析;按照“分类考核、兼顾公平、多劳多得”的原则,压力下移,以氯化铵蒸发量、包装量、蒸汽消耗量、各种材料动力消耗为抓手,降低成本,减亏脱困;班子成员和职能管理人员根据分工,强化管理,落实责任,要求“日事日清、日事日成”,分类考核,推进全方位对标。
对标赶超永远在路上
推行对标管理,就是要把企业的目光紧紧盯住业界最好水平,明确自身与业界最佳的差距,从而指明工作的总体方向。标杆除了是业界的最好水平以外,还可以将企业自身的最好水平作为内部标杆,通过与自身相比较,还可以增强自信,不断超越自我,从而能更有效地推动企业向业界最好水平靠齐。
试剂车间经过当前与自身指标的对比,氯化铵蒸汽单耗由11.31t/t下降至9.07t/t,吨氯化钠下降2.24吨蒸汽,折合动力费用313.6元/吨;废水蒸汽单耗由0.59t/m3下降到0.51t/m3,对标赶超活动开展以来,车间已累计降低成本74.56万元。

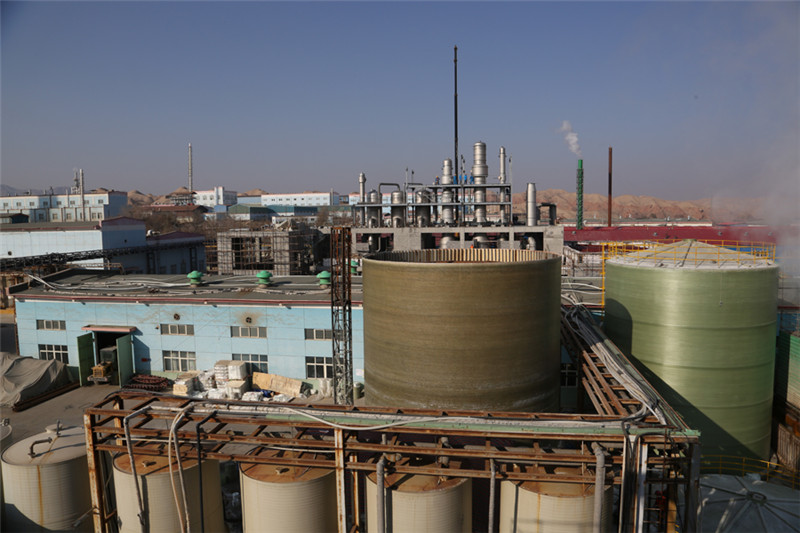

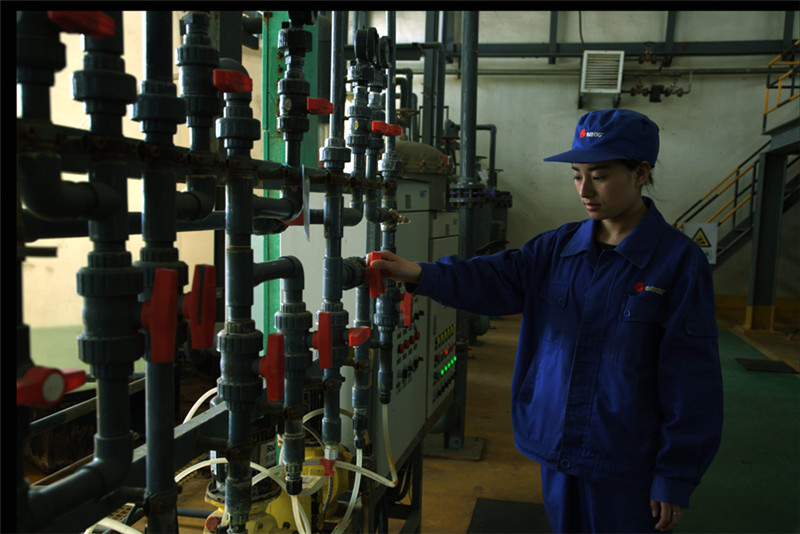
对标赶超无终点。下一步,试剂车间将借助公司《氨氮废水资源化利用升级改造项目》,发挥项目组及工程技术人员的作用,用心筹划、积极推进,组织全体员工在做好当前生产任务的前提下,全程参与到项目建设、安装调试及试运行工作中去,争取使项目发挥最大的效益,实现氨氮废水的资源化利用和全处理零排放,确保项目早日达产达标及稳定运行,真正意义上做到公司氨氮废水处理的资源化利用,从而实现与华美、和发先进指标的对标。同时,试剂车间也着力尽早筹划氯化铵后续衍生产业发展,开发附加值高的试剂级氯化铵产品研发和复合肥产业的研究,延伸产业链,使公司氨氮废水处理实现从单一的环保处理设施转变成氯化铵产业链,为公司的发展做出最大的贡献。
他们正以贯彻落实2019年《行政工作大纲》为起点,加快筹备氨氮废水项目的人员上岗前培训,用新思路、新举措推动对标赶超工作再上新台阶。
撰稿:邓家恂、赵宗英、王力霞、崔玉皎
摄影:郭利民